The Russian Lathe Accident shocked people worldwide with its tragedy. A factory worker named Marat was operating a lathe machine. While working, his clothes got caught in the spinning machine. Within seconds, the powerful lathe pulled him in completely.
The accident led to his untimely death at the KAMAZ PJSC factory in Russia. The video of the accident was leaked online, sparking massive reactions. People expressed shock and sadness over the tragic event. Many blamed poor workplace safety measures for the accident.
The lathe machine lacked proper safety features to protect the worker. The Russian authorities launched an investigation into the incident. This accident is now widely discussed in workplace safety forums.
It serves as a reminder of the dangers of industrial work. Safety equipment and proper training could have prevented such a loss. The tragedy emphasizes the importance of prioritizing safety in industrial workplaces.
Table of Contents
Overview of the Russian Lathe Accident
The Russian lathe accident was a tragic workplace incident. A worker named Marat was operating a lathe machine. During his work, his clothes got caught in the machine. This caused him to be pulled violently into the spinning mechanism.
The accident resulted in fatal injuries and his untimely death. The tragic event was captured on factory surveillance footage. This video later spread online, shocking people worldwide. The accident happened at KAMAZ PJSC, a Russian truck manufacturing company.
It raised many questions about workplace safety standards. The factory faced criticism for a lack of proper precautions. Many felt that more safety measures could have saved Marat’s life.
This tragedy highlights the dangers of working with heavy machinery. It serves as a reminder of the importance of safety protocols. Such incidents should encourage stricter enforcement of workplace safety rules.
Details of the Fatal Lathe Machine Incident in Russia
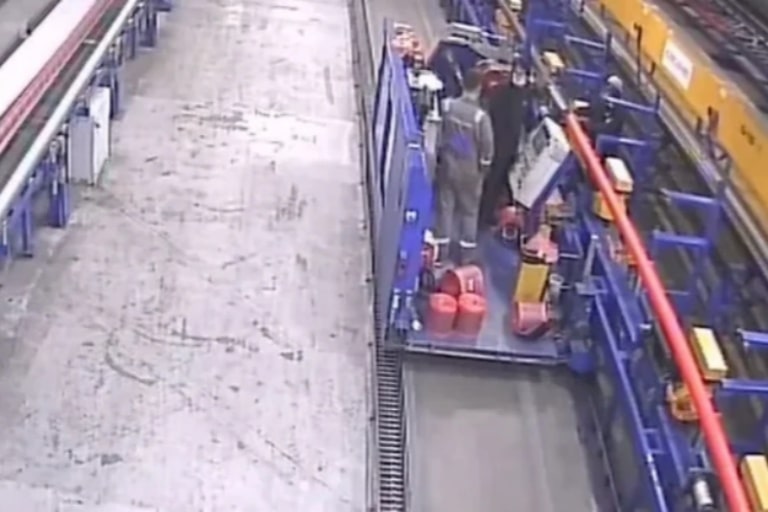
The fatal accident occurred at KAMAZ PJSC, a major factory in Russia. Marat, a 65-year-old worker, was operating a lathe machine. While working, his clothing got tangled in the spinning mechanism. The machine pulled him in with great force, causing fatal injuries.
Unfortunately, no one could stop the machine in time to save him. The incident was recorded by factory cameras and later leaked online. This brought the accident to the attention of a global audience. Investigations revealed gaps in the safety measures at the factory.
The lack of emergency stop mechanisms and protective gear was criticized. Experts believe such precautions could have prevented the tragedy. The factory’s management faced scrutiny over worker safety policies.
The accident sparked debates about industrial safety standards. It also raised awareness of the importance of proper worker training. This tragic incident is a stark warning for industries worldwide.
The Tragic Russian Lathe Accident: An Unforgettable Event
The Russian lathe accident left a lasting impact on many people. Marat’s tragic death shocked the world and sparked discussions. The footage of the incident showed the terrifying reality of industrial accidents. It revealed the risks faced by workers operating heavy machinery.
Marat was described as a kind and hardworking man by his colleagues. The factory failed to implement adequate safety measures for its workers. This led to the devastating loss of an experienced employee. The incident was not just a tragedy for Marat’s family but also a wake-up call.
Factories and industries need to prioritize their workers’ safety. Employers must ensure that equipment is safe to use at all times. The accident’s viral nature on the internet highlighted these issues further.
This unforgettable event reminds everyone of the human cost of negligence. It calls for urgent action to prevent such tragedies in the future.
Causes and Contributing Factors
- Lack of Proper Safety Training
Workers lacked proper training to operate complex machinery safely. They didn’t understand the risks involved with lathe machines. Safety training ensures everyone knows how to prevent accidents. Without it, workers face unnecessary dangers daily. This training could have saved lives in this tragedy.
- Inadequate Machine Maintenance
Machines were not inspected or serviced regularly to ensure safety. Worn-out parts can malfunction and cause dangerous accidents. Proper maintenance keeps machines running smoothly and prevents failures. Ignoring this step puts workers in harm’s way unnecessarily. This negligence likely played a role in this accident.
- Absence of Protective Clothing
Workers were not provided appropriate safety gear or clothing. Loose clothing can get caught in spinning machinery, causing harm. Protective gear minimizes risks and ensures safety during work. Employers must ensure workers wear proper attire for safety. This simple step could have saved lives.
- Ignored Emergency Stop Features
Emergency stop buttons were either unavailable or not functional. These features are crucial in preventing accidents during malfunctions. Workers should know how to stop machines immediately in danger. Neglecting this key safety measure invites unnecessary risks. An accessible stop feature could have saved Marat’s life.
- Overworked and Tired Employees
Excessive workloads can lead to exhaustion and poor focus. Tired workers are more prone to mistakes and accidents. Regular breaks and manageable hours help prevent these issues. Employers must value workers’ well-being and safety equally. Fatigue should never cost someone their life at work.
Understanding the Dangers of Lathe Machines: The Russian Incident
Lathe machines are powerful tools used in many industries. They shape materials like metal and wood but are extremely dangerous. The Russian lathe accident is a tragic example of these dangers. Marat’s clothing got caught in the machine, leading to his death.
This incident shows how small mistakes can have devastating results. Operating lathe machines requires proper training and safety precautions. Workers must wear protective clothing and avoid loose garments. Machines should have emergency stop buttons to prevent fatal accidents.
Employers must also conduct regular maintenance checks on machinery. The Russian incident highlights the importance of enforcing strict safety rules.
It serves as a lesson for industries to never overlook safety measures. The dangers of lathe machines are real and life-threatening. Understanding these risks can help prevent future tragedies. This heartbreaking event is a reminder of why safety comes first.
Workplace Safety Concerns Highlighted by the Russian Lathe Accident
The Russian lathe accident raised serious concerns about workplace safety. It exposed flaws in the safety standards at KAMAZ PJSC. Marat’s death could have been prevented with better precautions. The lack of protective clothing and emergency mechanisms was evident.
Factories must provide proper training for workers handling heavy machinery. Employers should also ensure that safety equipment is readily available. Regular inspections and maintenance are vital to prevent mechanical failures.
This accident highlighted the need for strict enforcement of safety policies. Workers should feel secure in their workplace, and not at risk of harm. The incident also sparked global discussions about industrial safety practices.
Many called for stricter laws to protect workers in dangerous jobs. Marat’s tragic death serves as a reminder of these critical issues. Improving workplace safety can save lives and prevent similar tragedies. Safety should always be a top priority for employers and industries.
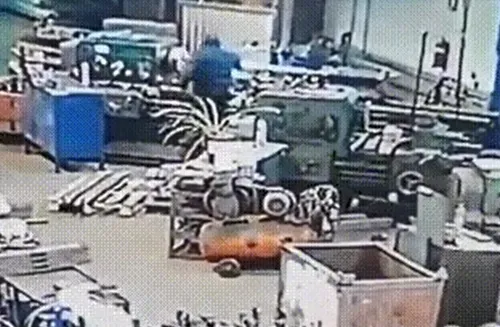
Analysis of Machinery Safety Protocols Post-Russian Lathe Incident
- Mandatory Use of Advanced Safety Features
New machines are required to include emergency stop buttons. Safety sensors and alarms are now mandatory features in factories. Workers can stop machines quickly during emergencies. These upgrades reduce risks and save lives in dangerous settings. Modern machines are safer than ever after this incident.
- Standardized Safety Training Protocols
Governments created mandatory safety training programs for workers. Every employee learns how to operate machinery safely. Factories must document and certify worker participation in training. These standardized programs promote safety awareness among staff. Trained workers make fewer mistakes, ensuring safer work environments.
- Regular Inspections by Regulatory Authorities
Factories now undergo routine inspections by government officials. Inspectors check machinery, safety gear, and working conditions thoroughly. Failing an inspection leads to fines or suspension of operations. These checks ensure workplaces prioritize safety over profits. Inspections reduce the chances of repeated accidents.
- Adoption of Ergonomic Machinery Designs
Manufacturers design machines that prioritize worker safety and comfort. New designs minimize risks of entanglement or improper usage. Ergonomic machines are easier to use and maintain safely. These changes reduce worker fatigue and improve operational efficiency. Safer designs emerged after the Russian lathe accident.
- Strict Penalties for Non-Compliance
Companies face heavy penalties for ignoring safety regulations. Fines, lawsuits, and shutdowns ensure compliance with new protocols. Employers are legally bound to provide safe environments for workers. Non-compliance damages reputations and leads to legal troubles. Fear of penalties drives industries to adopt safer practices.
Investigations Following the Russian Lathe Machine Fatality
The Russian lathe accident shocked everyone and demanded investigations. Authorities quickly started inquiries to understand what went wrong. They checked the machine’s condition and looked for safety rule violations. Investigators also interviewed coworkers and reviewed security footage for details.
The factory faced scrutiny for possibly neglecting worker safety. Questions arose about whether employees received proper training on machinery use. Experts examined if the equipment had proper emergency stop mechanisms.
The Russian Investigative Committee found gaps in enforcing workplace safety measures. They focused on preventing future accidents through stricter rules. Families of victims demanded justice and improved industrial standards. This tragic accident highlighted how small mistakes could lead to big disasters.
Everyone realized the importance of creating safer environments for workers. The investigation taught industries that prevention is always better than reacting too late. Every workplace must focus on safety to protect lives and prevent such tragedies.
Preventing Lathe Machine Accidents: Lessons from Russia
Preventing accidents like the Russian lathe tragedy is vital. Workers should receive proper training before handling dangerous machinery. Clear safety guidelines must be followed at all times. Employers should ensure all machines are well-maintained and inspected regularly.
Safety gear, like gloves and aprons, should always be mandatory. Emergency stop buttons on machines are critical for safety. Employers should also conduct regular safety drills for all employees. Supervisors must closely monitor workers to spot risks early.
Proper lighting in workplaces can prevent many unnoticed hazards. Encouraging workers to report unsafe conditions is essential. Industries must create a culture where safety comes first. The tragedy in Russia showed how neglecting safety can cost lives.
Employers and workers must work together to prevent such incidents. Learning from this event, every company should prioritize safety over speed or profits. Safer workplaces save lives and improve trust within industries.
Workplace Safety: A Crucial Responsibility
Workplace safety isn’t just rules; it’s about saving lives. Every company must prioritize safety as a core value. Workers deserve environments where they can perform without fear. Safety begins with training all employees about possible risks.
Proper signage and instructions make rules clear for everyone. Machines must have guards and emergency buttons to prevent harm. Employers should conduct inspections to identify and fix hazards. Providing protective gear like helmets and gloves is non-negotiable.
Safe work practices build trust and boost employee morale. Supervisors play a key role in ensuring rules are followed. Employers must invest in safety measures, not cut corners.
The Russian lathe tragedy showed the consequences of ignoring safety. Safety isn’t an extra task; it’s a daily commitment. Protecting workers should never be compromised for profit or speed. When workplaces value safety, accidents are reduced, and lives are saved.
The Human Cost: Emotional and Psychological Impact
Workplace accidents don’t just hurt bodies; they break spirits. The Russian lathe tragedy deeply affected the victim’s family. Losing a loved one in such a way causes immense grief. Coworkers who witnessed the event also faced trauma and fear.
Many struggled with feelings of guilt, even if they weren’t responsible. Emotional scars from such accidents last longer than physical injuries. Employers often underestimate the psychological effects on their teams. Families also face financial struggles after losing the primary earner.
Coworkers may feel unsafe or lose trust in their workplace. Counseling should be offered to help employees cope with trauma. Support groups can help families recover emotionally and financially. Every accident is a reminder of the human cost of neglect.
Workers deserve not just safety but also respect and care. Preventing accidents ensures not only lives but also mental peace. Prioritizing safety protects everyone, emotionally and physically.
Eyewitness Accounts of the Russian Lathe Machine Tragedy
Witnesses of the Russian lathe accident recall the horrific scene. They described how quickly the tragedy unfolded in seconds. A coworker saw Marat’s clothing caught in the spinning machine. Others nearby rushed to stop the lathe but couldn’t save him.
Witnesses reported hearing screams and seeing the machine’s violent motion. Some froze in shock, while others called for immediate help. The factory’s lack of an emergency stop made things worse. Witnesses later shared feelings of helplessness and lasting fear.
Many questioned why safety measures weren’t in place earlier. Their accounts revealed gaps in the company’s safety protocols. These stories are heartbreaking reminders of why safety is crucial.
The tragedy could have been prevented with better precautions. Eyewitnesses demand stricter rules to ensure such events never repeat. Their voices highlight the need for safer, more responsible workplaces.
- Anuel Height in 2025: How Tall Is the Puerto Rican Singer?
- Jim Caviezel Net Worth in 2025: How Rich Is the Famous Actor?
- Deshae Frost Net Worth 2025: How Much Does He Make?
- Deebaby Age: How Old is the Inspiring Rapper in 2025?
- Kanel Joseph Age – How Old is the Popular YouTuber in 2025?
Global Reactions to the Russian Lathe Accident and Its Implications
The Russian lathe accident shocked people around the world. Many expressed grief and anger over the tragic loss. Workplace safety activists called for stricter global safety laws. Industrial experts highlighted the importance of regular equipment checks.
Social media spreads awareness about the risks of heavy machinery. Some countries reviewed their safety policies after hearing about the incident. Employers worldwide were reminded of their duty to protect workers.
The incident became a case study in safety training programs. Families of victims from similar accidents shared their stories online. Governments began to stress workplace inspections and proper safety gear. This tragedy became a wake-up call for industries everywhere.
It showed how neglecting safety standards can harm lives globally. Safer workplaces save not just lives but also companies’ reputations. The global reaction proved that such incidents should never be ignored. Every life lost is a reminder to do better.
Learning from Tragedy: Recommendations and Best Practices
- Regular Machine Inspections
Every machine must be inspected and maintained regularly. Inspections help identify worn parts and prevent failures. Fixing issues early can stop accidents before they happen. Factories must follow strict schedules for machine checks. Regular care keeps workers safe and machines reliable.
- Comprehensive Safety Training Programs
Safety training must be mandatory for all factory workers. Workers should know how to handle machines and risks. Regular workshops can refresh their knowledge and awareness. Employers must ensure that every employee knows safety rules. Training helps build a culture focused on workplace safety.
- Strict Enforcement of Safety Gear
Every worker must wear safety gear, including tight clothing. Employers should provide protective equipment to all staff. Regular checks should ensure everyone follows the dress code. Gear like gloves, helmets, and glasses save lives daily. This simple practice reduces the chance of fatal accidents.
- Installation of Emergency Stop Systems
Emergency stop buttons must be on all industrial machines. Workers should be trained to use them effectively during emergencies. Employers must test these systems regularly to ensure they work. Accessible stops give workers control during dangerous situations. Such systems can prevent tragedies like Marat’s accident.
- Improved Work-Life Balance Policies
Employers must manage work hours to prevent fatigue. Tired employees are more prone to mistakes and accidents. Regular breaks and reasonable shifts improve focus and productivity. A well-rested workforce creates a safer work environment. Health and safety go hand in hand for better results.
Impact of the Russian Lathe Accident on Industrial Safety Standards
- Increased Awareness About Workplace Safety
This accident highlighted the risks of unsafe industrial practices. Companies now focus more on providing proper safety protocols. Media coverage spreads awareness about industrial accidents globally. Workers demand better training and equipment after such incidents. Tragedies often spark reforms that benefit future generations.
- Improved Machinery Standards Worldwide
Manufacturers updated machines to include better safety features. Emergency stops and alarms became a standard in factories. Safer machinery designs prevent incidents like this from recurring. New regulations ensure companies use updated equipment always. This accident pushed industries toward modernized, safer practices.
- Global Advocacy for Workers’ Rights
Workers started advocating for their safety and better rights. Unions pushed for stricter regulations and better working conditions. Governments created policies to ensure companies protect their employees. Companies with poor safety records faced heavy penalties globally. Workers’ voices became louder after this tragic accident.
- Implementation of Safety Audits
Industries now conduct regular safety audits to check compliance. Auditors review processes to ensure machines and staff follow rules. Unsafe practices and poor conditions are flagged and corrected. Audits also hold companies accountable for their employees’ safety. These evaluations reduce the risk of future accidents.
- Strengthened Employer Accountability
Employers face stricter penalties for neglecting worker safety. The accident emphasized the importance of employer responsibility. New laws hold companies accountable for unsafe environments. Worker compensation policies have improved globally since then. Accountability became a key focus in the industrial world.
Factors to Consider Before Operating Heavy Machinery
- Wear Proper Safety Gear
Always wear safety equipment like gloves, goggles, and helmets. Ensure your clothing fits tightly to prevent getting caught in machines. Loose clothes or accessories like jewelry can lead to serious injuries. Use steel-toed boots to protect your feet from heavy objects. Following these precautions can greatly reduce the risk of accidents.
- Understand the Machine’s Operation
Read and understand the machine’s manual before use. Attend training sessions to learn how to operate the equipment safely. Check controls and switches to ensure they are functioning properly. Understand emergency procedures to respond quickly during accidents. Familiarity with the machine reduces errors and improves safety.
- Inspect Machinery Before Use
Check for wear, damage, or loose parts before starting. Look for oil leaks, frayed wires, or strange noises. Confirm all safety guards are in place and secure. A quick inspection can help detect issues before they become hazards. Regular maintenance ensures the machine runs smoothly and safely.
- Stay Alert and Focused
Avoid distractions like talking, texting, or listening to music. Always stay aware of your surroundings and other workers nearby. Never operate machinery under the influence of alcohol or drugs. Fatigue can impair judgment, so take breaks if necessary. A clear mind ensures better decision-making and safer operations.
- Know Emergency Procedures
Learn how to stop the machine in an emergency quickly. Identify the location of emergency shut-off buttons or switches. Keep a fire extinguisher and first-aid kit nearby at all times. Inform coworkers of the emergency protocols for immediate response. Proper preparation can save lives in dangerous situations.
Frequently Asked Questions about Russian Lathe Accident
What Happened in the Russian Lathe Accident?
A factory worker named Marat was caught in a lathe machine. His clothing became entangled in the spinning mechanism, leading to fatal injuries. The tragic incident occurred at KAMAZ PJSC in Russia. It highlighted the dangers of improper safety measures in industrial settings. The incident has since raised awareness about workplace safety.
Was the Accident Captured on Video?
Yes, the incident was recorded on factory surveillance cameras. The graphic footage later leaked online and went viral. It sparked widespread discussions about industrial safety worldwide. Many criticized the lack of safeguards that could have prevented the tragedy. The video serves as a grim reminder of workplace hazards.
What Were the Main Causes of the Accident?
The accident occurred due to inadequate safety measures and training. Marat’s clothing became entangled, which could have been prevented with proper attire. The lack of protective barriers around the machine was also a factor. Poor enforcement of workplace safety rules contributed significantly. The incident underscores the importance of safety protocols.
What Actions Were Taken After the Accident?
The Russian Investigative Committee launched an inquiry into the incident. Officials reviewed safety procedures and interviewed coworkers at the factory. Discussions about stricter industrial safety laws began after the tragedy. KAMAZ PJSC faced scrutiny for not ensuring employee safety. The accident prompted calls for better training and equipment inspections.
Could the Accident Have Been Prevented?
Yes, proper safety measures could have prevented the incident. Wearing fitted clothing and using protective barriers around the machine would help. Regular inspections and training could identify and fix safety gaps. Strict adherence to industrial safety protocols is essential. Prevention is always better than facing such tragedies.
How Has the Incident Affected Workplace Safety Awareness?
The accident has sparked global discussions about industrial safety. Companies are re-evaluating their safety policies and training programs. Workers have become more aware of potential hazards in their roles. The incident also highlights the importance of reporting unsafe practices. Awareness is the first step toward preventing future accidents.
What Lessons Can Be Learned from This Tragedy?
The tragedy teaches the importance of prioritizing safety in workplaces. Employers must enforce strict safety rules and conduct regular training. Workers should wear appropriate gear and stay alert while operating machines. Emergency protocols should be easily accessible to all employees. The incident emphasizes the cost of negligence in workplace safety.
Conclusion about Russian Lathe Accident
The Russian lathe accident is a tragic reminder of workplace dangers. A 65-year-old factory worker, Marat, lost his life after being caught in a lathe machine. The accident occurred due to inadequate safety measures and improper clothing. Video footage of the incident sparked outrage and calls for better workplace protocols.
This incident highlights the importance of wearing safety gear, proper training, and regular equipment inspections. Companies must prioritize employee safety by enforcing strict safety policies. Workers, too, must stay alert, follow procedures, and report unsafe practices.
Such tragedies teach valuable lessons about industrial safety. The cost of neglecting safety measures can result in the loss of lives and significant emotional and financial impact. By taking proactive steps, accidents like this can be prevented in the future. This serves as a wake-up call for industries worldwide.